In our daily lives and across countless industries, we're constantly surrounded by products made from either steel or aluminum. From the towering skyscrapers that shape our cityscapes to the cars we drive and the cans that hold our favorite beverages, these two materials play a pivotal role. But when it comes to choosing between steel and aluminum for a particular application, the decision can be far from straightforward. Let's embark on a detailed exploration to determine which one might be the better fit for various needs.
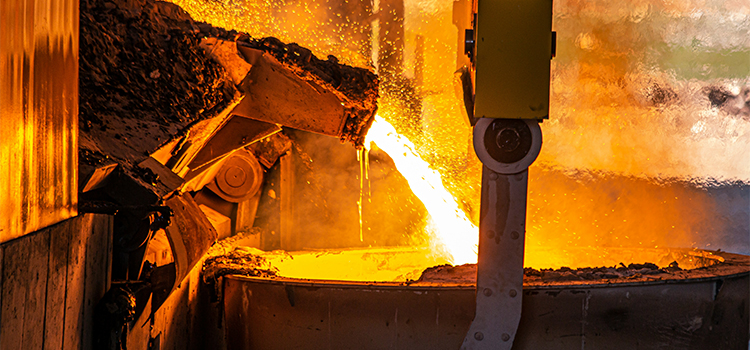
Steel and Aluminum: An Introduction
Steel
Steel is an alloy primarily composed of iron and carbon. The carbon content, typically ranging from 0.2% to 2.1% by weight, significantly influences its properties. There are numerous types of steel. Carbon steel, for example, is known for its strength and affordability. It's widely used in construction and manufacturing. Alloy steel, on the other hand, has additional elements like manganese, chromium, or nickel added to enhance specific properties such as hardness, toughness, or corrosion resistance. Think of the robust I - beams used in building construction or the durable stainless - steel utensils in your kitchen - these are all products of steel's versatility.
Aluminum
Aluminum is a lightweight metal that's abundant in the Earth's crust. It's usually found in bauxite ore and requires a significant amount of energy to extract. Aluminum in its pure form is relatively soft, but when alloyed with elements like copper, magnesium, or zinc, it becomes much stronger. Common aluminum alloys include 6061, which is widely used in general - purpose applications like automotive parts and 7075, known for its high strength and often used in aerospace components. Look around, and you'll spot aluminum in everyday items like beverage cans, window frames, and even in high - end electronics.
Physical Properties Showdown
Density
One of the most striking differences between steel and aluminum is their density. Steel typically has a density of around 7.85 grams per cubic centimeter. In contrast, aluminum's density is approximately 2.7 grams per cubic centimeter. This significant difference makes aluminum much lighter. In the aviation industry, for instance, every kilogram of weight reduction can lead to substantial fuel savings over the lifespan of an aircraft. That's why aluminum is the material of choice for constructing aircraft bodies and wings. However, in applications where weight is not a concern, and stability due to mass is required, such as in some types of industrial machinery or the foundations of large structures, steel's higher density can be an advantage.
Strength
Steel is renowned for its high strength. High - carbon steel and alloy steels can achieve extremely high tensile strengths, making them ideal for applications where structural integrity under heavy loads is crucial. For example, the suspension bridges that span vast waterways rely on steel cables and beams to withstand the weight of traffic and environmental forces. Aluminum alloys, though, have also made great strides in strength. Some high - strength aluminum alloys, like those used in aerospace, can rival the strength - to - weight ratio of certain steels. In the automotive industry, aluminum is increasingly being used in body structures to reduce weight while still maintaining safety standards, as advancements in alloy technology have improved its strength properties.
Conductivity
When it comes to electrical and thermal conductivity, aluminum outshines steel. Aluminum is an excellent conductor of electricity, which is why it's commonly used in power transmission lines. It offers a good balance between conductivity and cost, especially when compared to more expensive conductors like copper. In terms of thermal conductivity, aluminum's ability to transfer heat quickly makes it a popular choice for heat sinks in electronic devices. For example, the cooling fins on a computer's CPU are often made of aluminum alloy to efficiently dissipate heat and prevent overheating. Steel, while it can conduct electricity and heat, does so at a much lower rate, making it less suitable for applications where high conductivity is essential.
Chemical Properties: A Closer Look
Corrosion Resistance
Steel has a Achilles' heel when it comes to corrosion. In the presence of oxygen and moisture, steel readily undergoes oxidation, forming rust. This can weaken the structure over time. To combat this, various protective measures are employed, such as painting, galvanizing (coating with zinc), or using stainless steel, which contains chromium that forms a passive oxide layer. Aluminum, on the other hand, has a natural advantage. When exposed to air, it forms a thin, dense oxide layer on its surface. This layer acts as a barrier, preventing further oxidation and corrosion. This makes aluminum highly suitable for outdoor applications, such as in coastal areas where the salty air can be particularly corrosive. For example, aluminum fences and outdoor furniture can withstand years of exposure to the elements without significant degradation.
Chemical Reactivity
Aluminum is a relatively reactive metal. In certain conditions, it can react vigorously, especially with acids. However, the protective oxide layer that forms on its surface under normal conditions inhibits most reactions. In some industrial processes, the reactivity of aluminum can be harnessed. For example, in the production of certain chemicals, aluminum can be used as a reducing agent. Steel, in comparison, is less reactive under normal circumstances. But in high - temperature or highly acidic/basic environments, it can undergo chemical reactions that may affect its integrity. For instance, in some chemical plants, special grades of steel are required to resist the corrosive effects of harsh chemicals.
Comparison of Processing Performance
Forming and Processing
Steel provides a wide variety of forming options. Forging is a common method in which the metal is heated and shaped by applying compressive forces. This is perfect for manufacturing strong and complex-shaped parts, like the crankshafts in engines. Rolling is another process where steel is passed through rollers to produce sheets, plates, or various profiles. The automotive industry frequently uses stamping, a type of cold-forming process, to create car body panels from steel sheets. Aluminum is also highly malleable and can be easily formed. Extrusion is a popular process for aluminum, during which the metal is forced through a die to create long and uniform shapes. This is how aluminum window frames are manufactured. Die-casting is also widely applied to aluminum, enabling the production of intricate and detailed parts, such as the engine blocks in many modern cars.
Welding Performance
Welding steel can be a complicated process. Different types of steel demand specific welding techniques and filler materials. For instance, carbon steel can be welded using methods like arc welding, but precautions must be taken to prevent problems such as hydrogen embrittlement, which can weaken the welded joint. Due to its alloying elements, stainless steel may require special electrodes to ensure a strong and corrosion-resistant weld. On the other hand, aluminum welding presents its own difficulties. Aluminum has a high thermal conductivity, meaning it dissipates heat rapidly during the welding process. This requires higher heat inputs and specialized welding equipment, such as tungsten inert gas (TIG) welding or metal inert gas (MIG) welding. Moreover, the oxide layer on aluminum needs to be removed before welding to ensure a proper bond.
Cost Considerations
Raw Material Cost
The cost of steel is relatively stable. Iron ore, the main raw material for steel production, is abundant in many parts of the world. The cost of mining and processing iron ore, together with the relatively simple process of converting it into steel, contributes to its affordability. However, aluminum has a more complex and energy-intensive production process. Bauxite ore needs to be refined into alumina, and then electrolysis is used to extract pure aluminum. This high energy requirement, along with the cost of mining and refining bauxite, generally makes the raw material cost of aluminum higher than that of steel.
Processing Cost
Steel's well-established and widespread manufacturing processes mean that, in many cases, the processing cost can be relatively low, especially for large-scale production. However, if complex shapes or high-precision machining are needed, the cost can increase significantly. In some aspects, aluminum processing can be more expensive. Although it is easy to form into complex shapes, the need for specialized equipment for processes like extrusion and the challenges of welding can drive up the cost. For example, setting up an extrusion line for aluminum requires a substantial investment in equipment and tooling.
Overall Cost Consideration
When considering the overall cost, it's not just about the raw material and processing costs. The lifespan and maintenance requirements of the final product also play an important role. For example, a steel structure may need regular painting and maintenance to prevent corrosion, which adds to the long-term cost. An aluminum structure, with its better corrosion resistance, may have lower maintenance costs over time. In some applications, such as the construction of a large-scale industrial building, the lower raw material and processing costs of steel may make it more cost-effective. In other cases, like in the production of high-end consumer electronics, where the lightweight and corrosion-resistant properties of aluminum justify the higher cost, aluminum may be the preferred choice.
Diverse Applications
Construction Field
In the construction industry, steel is a crucial material. Its high strength and load-bearing capacity make it essential for building the frames of skyscrapers and large commercial buildings. Steel beams and columns can support huge amounts of weight, allowing for the construction of tall and open-plan structures. Bridges also rely heavily on steel. Suspension bridges, with their long spans, use steel cables and trusses to distribute the load. On the contrary, aluminum is often used for more aesthetic and lightweight applications. Aluminum windows and doors are popular because of their modern appearance, energy efficiency, and corrosion resistance. Aluminum curtain walls can give buildings a sleek and contemporary look while also being lightweight, reducing the load on the building's structure.
Automotive Industry
Steel has long been the dominant material in the automotive industry. It is used in the chassis, body frames, and many mechanical components because of its high strength, which is vital for safety. However, as the industry moves towards more fuel-efficient vehicles, aluminum is becoming more widely used. Aluminum is used in engine blocks, which reduces the weight of the engine and, in turn, improves fuel economy. It is also increasingly used in body panels to reduce the overall weight of the vehicle without sacrificing safety, as modern aluminum alloys can provide the necessary strength.
Aerospace Field
Steel has long been the dominant material in the automotive industry. It is used in the chassis, body frames, and many mechanical components because of its high strength, which is vital for safety. However, as the industry moves towards more fuel-efficient vehicles, aluminum is becoming more widely used. Aluminum is used in engine blocks, which reduces the weight of the engine and, in turn, improves fuel economy. It is also increasingly used in body panels to reduce the overall weight of the vehicle without sacrificing safety, as modern aluminum alloys can provide the necessary strength.
Daily Use Products Field
In our daily lives, we often come across both steel and aluminum products. Steel is commonly used in kitchen knives, where its hardness and edge-retention properties are highly appreciated. Furniture made of steel, such as metal chairs and tables, can be both sturdy and fashionable. On the other hand, aluminum can be found in items like lightweight cookware, which heats up quickly and evenly. Electronic devices, such as laptops and tablets, often have aluminum cases due to their sleek appearance, lightweight design, and good heat dissipation properties.
Making the Right Choice
Choosing According to Performance Requirements
If you need a material with high strength and stiffness for a load-bearing structure, steel is probably the better option. For example, in a large industrial warehouse where heavy machinery will be stored, steel beams can provide the necessary support. However, if weight reduction is a top priority, such as in a portable electronic device or a racing car, aluminum's low density makes it a more suitable choice. When it comes to conductivity, if you are working on an electrical or thermal application, aluminum should be your first consideration.
Choosing According to Cost Budget
For projects with a limited budget, steel may be the more economical choice, especially considering its lower raw material cost and generally lower processing costs for simple shapes. However, if you can afford a higher upfront cost and are looking for long-term savings in terms of maintenance and performance, aluminum might be a worthwhile investment. For example, in a coastal area where corrosion is a major concern, an aluminum structure may cost more initially but will save money in the long term due to its superior corrosion resistance.
Choosing According to Application Scenarios
In outdoor applications, especially in harsh environments, aluminum's corrosion resistance gives it an advantage. For example, outdoor signage or light poles made of aluminum will last longer without rusting. In high-temperature industrial settings, such as in a steel foundry or a power plant boiler, steel's ability to withstand high temperatures makes it the preferred material.
In conclusion, the age-old question of whether steel or aluminum is better does not have a universal answer. Both materials have their own unique set of properties, advantages, and disadvantages. By carefully considering the specific requirements of your project, whether it is performance, cost, or application-specific factors, you can make an informed decision. We would love to hear about your experiences in choosing between steel and aluminum. Please share your thoughts in the comments below!
Post time: Feb-17-2025