When choosing materials for construction, manufacturing, or DIY projects, aluminum and stainless steel are two of the most popular metals. But what exactly sets them apart? Whether you’re an engineer, a hobbyist, or simply curious, understanding their differences can help you make informed decisions. In this blog, we’ll break down their properties, applications, costs, and more—backed by expert sources—to help you choose the right material for your needs.
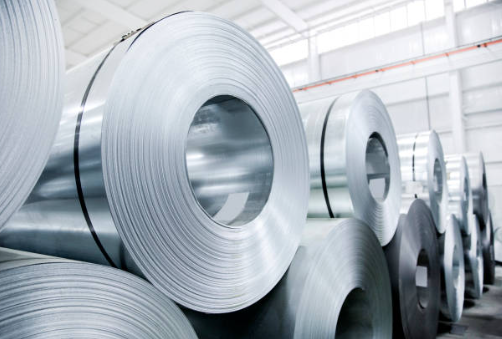
1. Composition: What Are They Made Of?
The fundamental difference between aluminum and stainless steel lies in their composition.
Aluminum is a lightweight, silvery-white metal found in the Earth’s crust. Pure aluminum is soft, so it’s often alloyed with elements like copper, magnesium, or silicon to enhance strength. For example, the widely used 6061 aluminum alloy contains magnesium and silicon.
Stainless Steel is an iron-based alloy containing at least 10.5% chromium, which creates a passive oxide layer to resist corrosion. Common grades like 304 stainless steel also include nickel and carbon.
2. Strength and Durability
Strength requirements vary by application, so let’s compare their mechanical properties.
Stainless Steel:
Stainless steel is significantly stronger than aluminum, especially in high-stress environments. For instance, grade 304 stainless steel has a tensile strength of ~505 MPa, compared to 6061 aluminum’s ~310 MPa.
Aluminum:
While less strong by volume, aluminum has a better strength-to-weight ratio. This makes it perfect for aerospace components (like airplane frames) and transportation industries where reducing weight is critical.
So, stainless steel is stronger overall, but aluminum excels when lightweight strength matters.
3. Corrosion Resistance
Both metals resist corrosion, but their mechanisms differ.
Stainless Steel:
Chromium in stainless steel reacts with oxygen to form a protective chromium oxide layer. This self-healing layer prevents rust, even when scratched. Grades like 316 stainless steel add molybdenum for extra resistance to saltwater and chemicals.
Aluminum:
Aluminum naturally forms a thin oxide layer, shielding it from oxidation. However, it’s prone to galvanic corrosion when paired with dissimilar metals in moist environments. Anodizing or coatings can enhance its resistance.
So, stainless steel offers more robust corrosion resistance, while aluminum requires protective treatments in harsh conditions.
4. Weight: Aluminum Wins for Lightweight Applications
Aluminum’s density is about 2.7 g/cm³, less than a third of stainless steel’s 8 g/cm³, which is very lightweight.
· Aircraft and automotive parts
· Portable electronics (e.g., laptops)
· Consumer goods like bicycles and camping gear
Stainless steel’s heft is an advantage in applications needing stability, such as industrial machinery or architectural supports.
5. Thermal and Electrical Conductivity
Thermal Conductivity:
Aluminum conducts heat 3x better than stainless steel, making it ideal for heat sinks, cookware, and HVAC systems.
Electrical Conductivity:
Aluminum is widely used in power lines and electrical wiring due to its high conductivity (61% of copper’s). Stainless steel is a poor conductor and is rarely used in electrical applications.
6. Cost Comparison
Aluminum:
Generally cheaper than stainless steel, with prices fluctuating based on energy costs (aluminum production is energy-intensive). As of 2023, aluminum costs ~$2,500 per metric ton.
Stainless Steel:
More expensive due to alloying elements like chromium and nickel. Grade 304 stainless steel averages ~$3,000 per metric ton.
Tip: For budget-friendly projects where weight matters, choose aluminum. For longevity in harsh environments, stainless steel may justify the higher cost.
7. Machinability and Fabrication
Aluminum:
Softer and easier to cut, bend, or extrude. Ideal for complex shapes and rapid prototyping. However, it can gum up tools due to its low melting point.
Stainless Steel:
Harder to machine, requiring specialized tools and slower speeds. However, it holds precise shapes and finishes well, suiting medical devices or architectural details.
For welding, stainless steel requires inert gas shielding (TIG/MIG), while aluminum demands experienced handling to avoid warping.
8. Common Applications
Aluminum Uses:
· Aerospace (aircraft fuselages)
· Packaging (cans, foil)
· Construction (window frames, roofing)
· Transportation (cars, ships)
Stainless Steel Uses:
· Medical instruments
· Kitchen appliances (sinks, cutlery)
· Chemical processing tanks
· Marine hardware (boat fittings)
9. Sustainability and Recycling
Both metals are 100% recyclable:
· Aluminum recycling saves 95% of the energy required for primary production.
· Stainless steel can be reused indefinitely without quality loss, reducing mining demand.
Conclusion: Which Should You Choose?
Choose Aluminum If:
· You need a lightweight, cost-effective material.
· Thermal/electrical conductivity is critical.
· The project doesn’t involve extreme stress or corrosive environments.
Choose Stainless Steel If:
· Strength and corrosion resistance are top priorities.
· The application involves high temperatures or harsh chemicals.
· Aesthetic appeal (e.g., polished finishes) matters.
Post time: Feb-25-2025