CNC Machining: Precision and Detail at Its Best
CNC (Computer Numerical Control) machining is a widely used technique in the modern production of aluminum cases, especially for precision components. With CNC machines, manufacturers can precisely cut, carve, and drill aluminum parts according to design specifications. This process ensures that every part meets strict requirements, resulting in high-precision components and refined finishes.
Impact on Product Quality
CNC machining offers high precision and consistency, ensuring the appearance and functionality of the aluminum case are well-maintained. For example, the installation of small components like latches and hinges can be done with great accuracy, ensuring smooth operation and long-lasting durability.
Impact on Cost
While CNC machining guarantees high-quality results, it comes at a higher cost. The machinery itself is expensive, and the skilled labor required for operation also adds to the overall cost. As a result, aluminum cases produced with CNC machining tend to be more costly. However, over the long term, the precision and quality of the parts help reduce the likelihood of repairs or defects, which can lower after-sales costs.
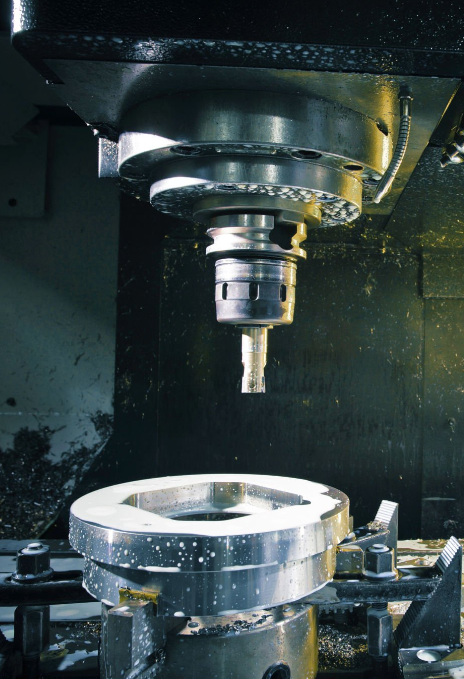
Die Casting: The Key to Complex Shapes
Die casting is a manufacturing process that involves injecting molten aluminum alloy into a mold under high pressure to create precise and complex shapes. This technique is often used for making the shell, corner protectors, and some of the more intricate internal structures of aluminum cases.
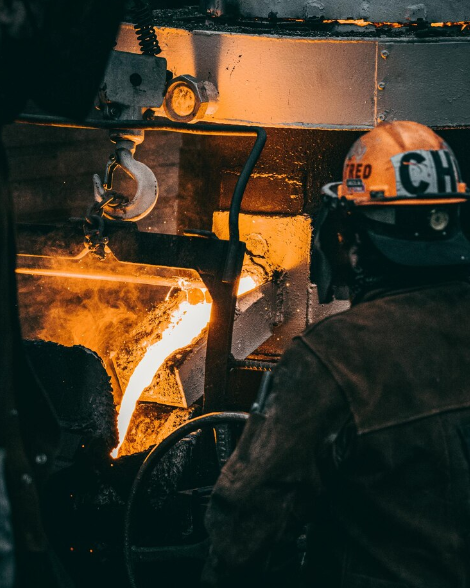
Impact on Product Quality
Die casting enables aluminum cases to have a robust and durable exterior, capable of withstanding external impacts and scratches. The molds are highly accurate, producing smooth surfaces that meet both aesthetic and functional requirements. However, because the process involves high temperatures and pressures, issues like air pockets or cracks can occasionally arise in the material.
Impact on Cost
The initial investment in die-casting molds can be high, and creating custom molds takes time. However, once the mold is made, the die casting process is highly efficient, making it suitable for mass production at a lower unit cost. If production volumes are low, the upfront mold costs can raise the overall price.
Sheet Metal Forming: Balancing Strength and Flexibility
Sheet metal forming is another commonly used process in aluminum case manufacturing, particularly for the production of the outer frame and large structural parts. This method involves applying mechanical pressure to shape aluminum sheets into the desired structure. It is typically used for parts that are less complex but require significant strength.

Impact on Product Quality
Sheet metal forming provides high strength and stability to the aluminum case, making it suitable for products that need to carry heavier loads or offer additional protection. The formed cases tend to be rigid, stable, and resistant to deformation, offering a solid structure.
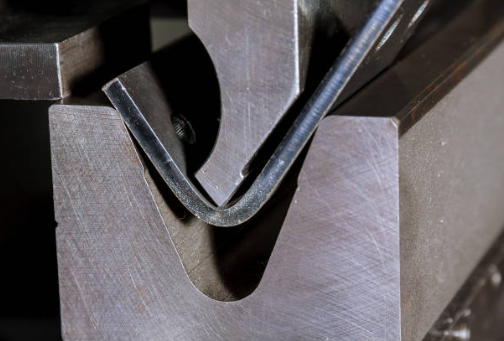
Impact on Cost
Sheet metal forming provides high strength and stability to the aluminum case, making it suitable for products that need to carry heavier loads or offer additional protection. The formed cases tend to be rigid, stable, and resistant to deformation, offering a solid structure.
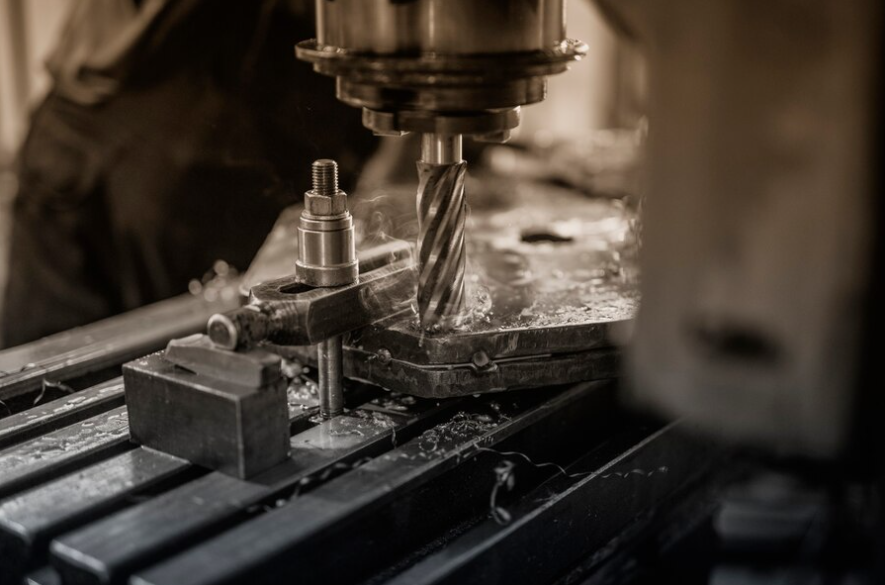
Conclusion: The Trade-Off Between Process and Cost
From the analysis above, it's clear that the manufacturing processes of aluminum cases directly determine their quality and cost. CNC machining provides high precision and is ideal for intricate parts, but it comes at a higher price. Die casting is suitable for large-scale production, enabling complex shapes to be created at lower per-unit costs, though it requires significant upfront investment in molds. Sheet metal forming strikes a good balance between cost and quality, especially for medium-complexity designs.
When choosing an aluminum case, it's essential to not only consider its appearance and functionality but also to understand the manufacturing processes behind it. Different processes suit different needs and budgets, so knowing how these methods affect both quality and cost can help you make a more informed decision.
I hope today's discussion gives you a deeper understanding of aluminum case manufacturing processes. If you have any further questions about the production of aluminum cases, feel free to leave a comment or reach out to me!
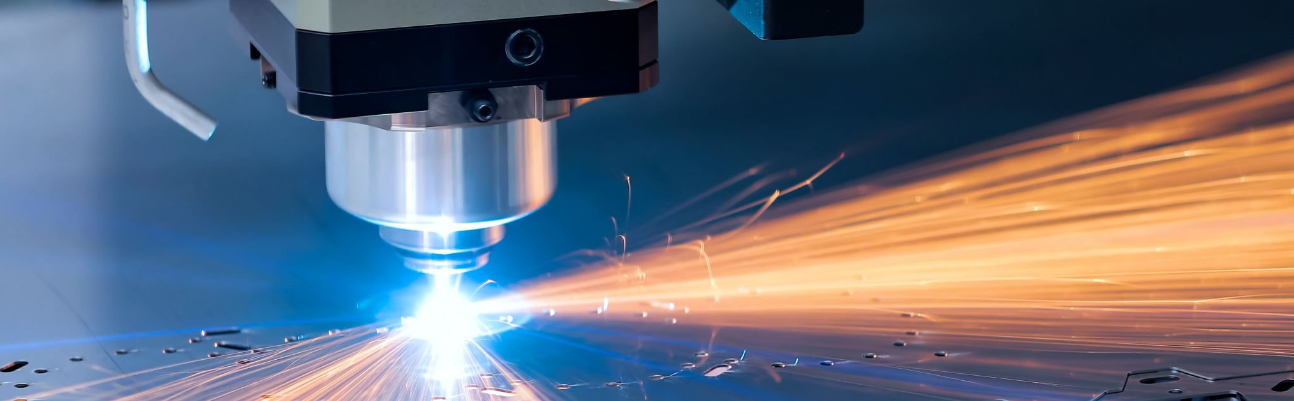
Everything you need you could contact us
Post time: Nov-13-2024